What will you find on this page?
- Overview: Inspecting the integrity of pharmaceutical product packaging and protecting health
- Pharmaceutical product packaging inspection methods including Headspace Gas Analysis, Automatic Visual Inspection, and Vacuum Decay & Pressure Decay testing
- Different packaging for new challenges: Types of products that can undergo inspection including pre-filled syringes, single-dose BFS vials, freeze-dried products, and viscous products
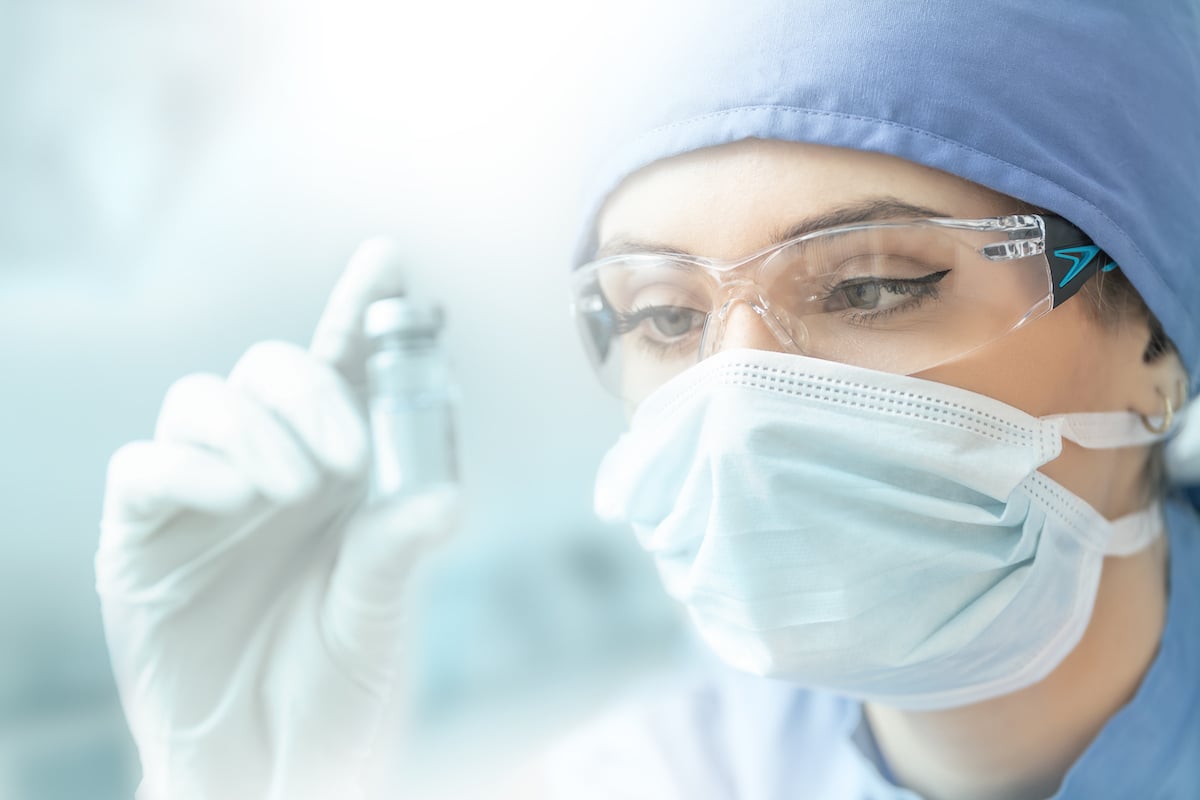
Overview: Inspecting the integrity of pharmaceutical product packaging and protecting health
Testing pharmaceutical products has always been a central step in the industrial process leading to their commercialization. Checking the proper seal of the packaging plays a fundamental role in manufacturing. Regardless of the type of product, it is essential to check that its container has no holes, micro-holes, cuts, incisions or inclusions and that the sealing process was completed properly. Non-compliant packaging can pose a number of risks, including:- Risk of dispersion of some of the product, which can lead to errors in the dosage of the active ingredient administered to the patient or to the sale of completely unusable drugs
- Risk of alteration and deterioration of the active ingredient, due to the presence of inert particles, moisture or gases inside the packaging that could cause oxidation and damage the product.
- Risk of contamination due to an error when closing the packaging which compromises the content, making it unusable and potentially unsafe for the user. This could indicate a more general malfunction of the production line with potentially serious consequences for the entire process.
Pharmaceutical product packaging inspection methods including Headspace Gas Analysis, Automatic Visual Inspection, and Vacuum Decay & Pressure Decay testing
Pharmaceutical packaging controls have developed significantly over the years. In the past, products were generally inspected using sample analysis. A few products were checked for packaging tightness, and if defects were found, the entire lot to which the defective product belonged was eliminated.
These tests were almost always destructive, which created many difficulties for manufacturers:
- Loss of all tested samples: even compliant products had to be eliminated because they were damaged during analysis.
- Loss of compliant products contained in the lot from which the non-compliant tested sample was extracted
- Risk of selling non-compliant products that had not been tested
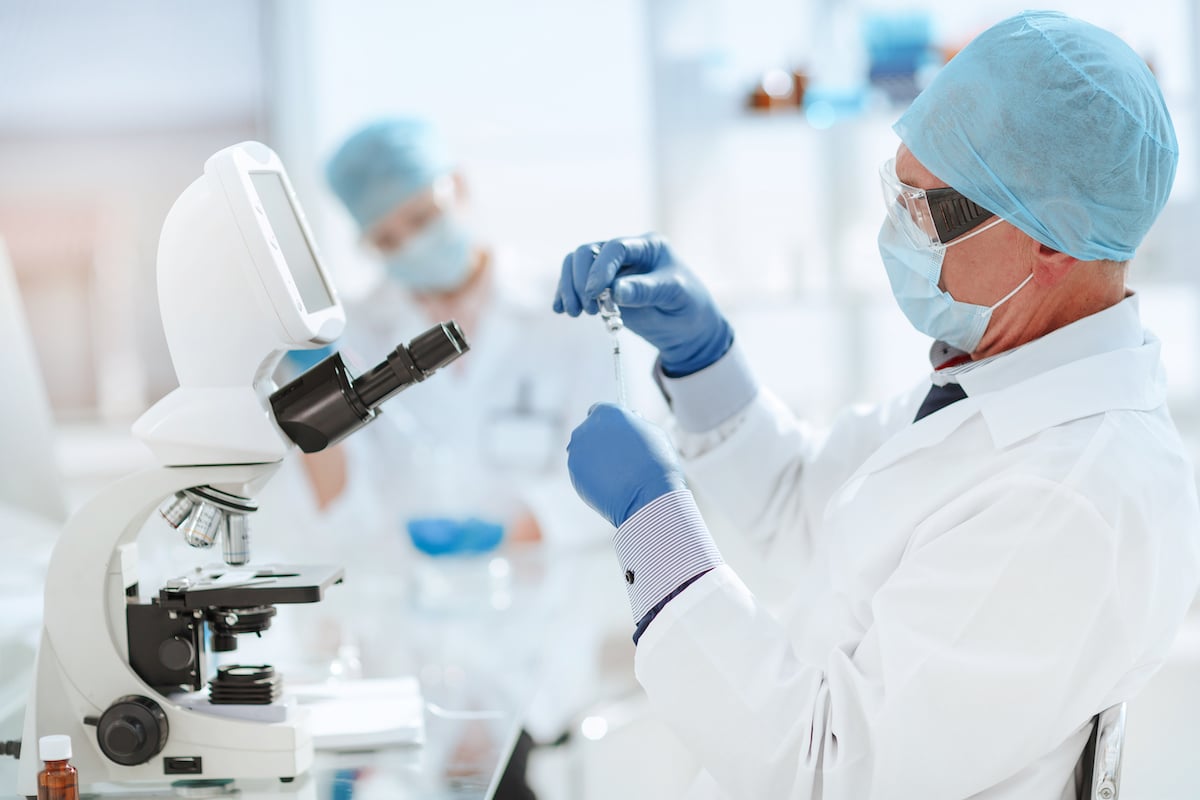
New leak testing methodologies have been developed to meet the pharmaceutical industry ‘s need to limit waste and to meet international regulatory authorities’ increasingly stringent demands. These new methods are not destructive and can be used for all products ready to be sold. This has significantly improved drug safety, reducing waste without endangering the health of future product users in any way.
Today’s analysis methods test 100% of products that have already been sealed, analysing a series of parameters that identify potential damage to the packaging. The most common types of test, are available in the machines designed, supplied and installed by Bonfiglioli Engineering
This test method inspects the integrity of a sealed product’s packaging by detecting the presence of certain gases in its “headspace”, i.e., the space inside the packaging not occupied by the product. The test checks that the sealed packaging contains no gas or moisture that could contaminate or damage the active ingredient, or whose presence would indicate the occurrence of an unexpected event at some point in the industrial process. The analysis is based on a tunable diode laser absorption spectrometer (TDLAS), which uses laser diodes tuned to the frequency of the molecule being sought. Once it has been tuned to the frequency of oxygen, carbon dioxide or nitrogen, the spectrometer measures the level of absorption of the laser to determine the quantity of that molecule inside the packaging and to check that the value matches the expected value. For products stored in a protective nitrogen atmosphere, for example, HGA ensures that the amount of oxygen present in the head space of the container is minimal, indicating that the nitrogen cleaning process has been completed successfully and there is no risk of product oxidation.
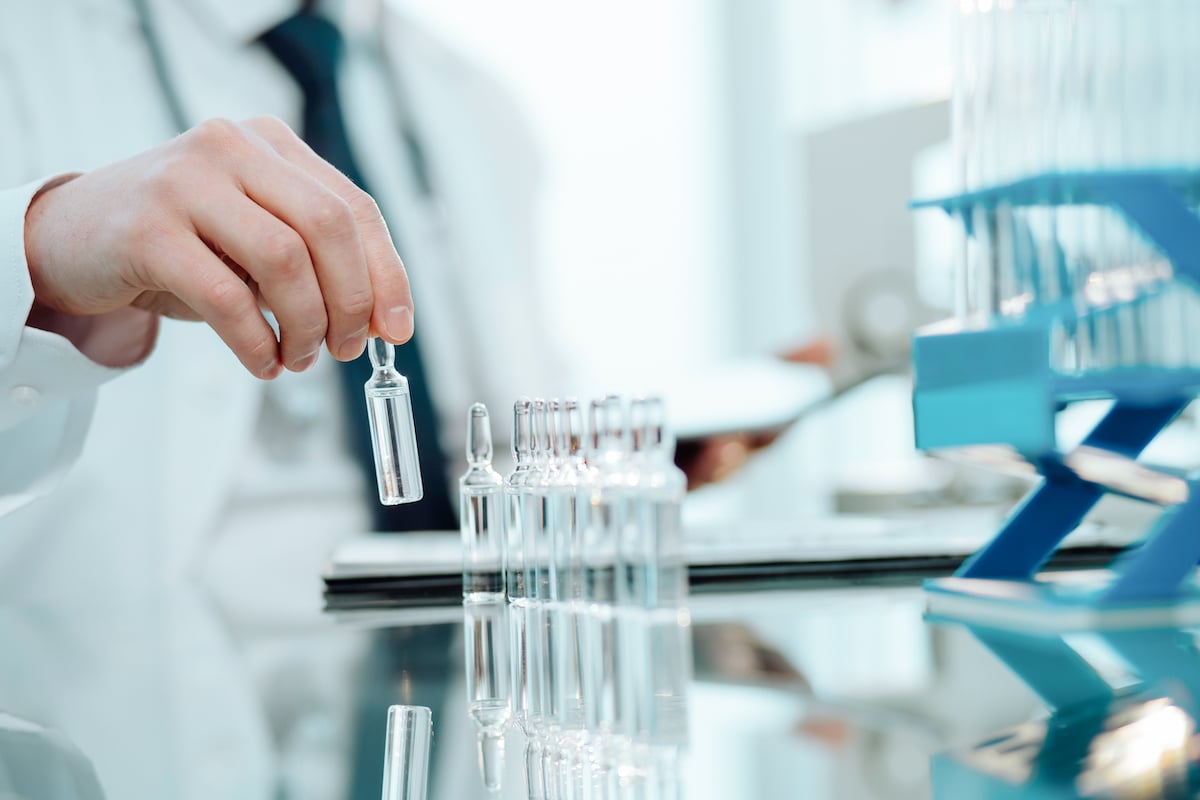
Automatic Visual Inspection (AVI):
This test method uses high-resolution cameras, lighting systems and software algorithms to photograph and then analyse products to detect holes, inclusions, cracks and cosmetic defects in their container. The test also detects possible defects in the contents, such as impurities or incorrect filling or colour levels.
This automated test uses a system of cameras to photograph the sample from several angles and in motion. Then, special software analyses the images and identifies any products that are damaged or defective so that they can be discarded automatically. This technology is currently undergoing further development based on the potential of artificial intelligence. Today’s highly evolved software systems can “learn from their mistakes” in order to provide faster and more accurate results.
Vacuum and Pressure Decay Method (VDM-PDM):
This type of test is easy to use on a wide range of products contained in both rigid and flexible packaging. It identifies the presence of holes and micro-holes in the surface of a sealed container by modifying the pressure conditions around the product, then taking two readings of the pressure value, a few seconds apart. Any difference between the two values greater than that set during machine configuration indicates that the product is either not intact or has been improperly sealed (in the most serious cases, the error can already be detected when the pressure is being modified) and must be eliminated.
Each of these types of test examines a different aspect of packaging integrity, so choosing one over another depends on what regulatory authorities recommend and how each individual production line is organised. The tests can also be combined for improve safety even further in special machines that verify the correct composition of the headspace (via HGA), the absence of holes (via VDM-PDM) and the absence of contaminants or inclusions in the bottle (via AVI) in sequence.
Different packaging for new challenges: Types of products that can undergo leak testing
Providing solutions to test the integrity of pharmaceutical packaging means addressing all the challenges of analysing new and diverse products. In the past, most products were contained in vials or rigid bottles with standard shapes. However, today's drug market proposes products that are increasingly complex and that require special solutions for proper handling and testing in the factory.
Specific machines have been built and implemented to test vials and bottles and complex products very accurately. These products include:
- Pre-filled syringes: Testing of these products is particularly important for two reasons. First, pre-filled syringes contain parenteral drugs that are injected directly into the patient's bloodstream, which requires a perfect package seal and integrity to prevent the contamination and dispersion of the active ingredient that could result in a dosage error when it is administered. Second, these types of products are designed to be used in conditions where hygiene and health conditions may not be optimal or where drugs must be administered very quickly (e.g., syringes containing vaccines that are distributed worldwide). So, the products must be sealed and stored properly to best meet the needs of the patients and the professionals administering the injections. Very close attention must be paid when handling the syringes during testing to avoid inadvertently pressing their piston, which would cause product loss and dosing errors.
- Single-dose BFS vials: These products are stored in a plastic vial that is “blown”, filled and sealed right inside the machine, minimising the need for human intervention. Testing is more complex because the container is not perfectly rigid, though VDM, AVI or, more rarely, HGA, can be added to complete the process.
- Freeze-dried products: Freeze-dried drugs offer countless advantages because the lyophilisation technique, in which the water contained inside a product is rapidly eliminated without radically modifying its structure, results in stable drugs that are easy to transport and store, and are ready to be re-hydrated and used whenever needed. Testing products of this type requires special care, because contamination or breakage could have very serious consequences, since freeze-dried products are often administered by injection once they are rehydrated. Again, freeze-dried products can also be inspected using HGA, AVI or PDM.
- Viscous products: The last category of products posing significant challenges during testing includes protein drugs and products containing viscous components that can form chains capable of temporarily plugging a hole in the container, distorting the result of a VDM control. In this case, combined machines that use HGA and AVI technologies as well offer a possible solution: a double test is the best way to prevent damaged products from being erroneously considered suitable for sale.